Learn what causes VT1000 pitting, how to prevent it, and the best solutions to protect your equipment from damage and ensure long-term reliability.
Table of Contents
Introduction
If you own or work with equipment that uses the VT1000, you may have encountered issues with pitting. Pitting is a common form of localized corrosion that can severely impact the performance and longevity of mechanical parts and components. Understanding why this happens and how to prevent it is crucial for anyone looking to maintain the health of their VT1000 system. In this post, we’ll explore what causes VT1000 pitting, how it affects your equipment, and the best practices for preventing and mitigating damage.
Want to protect your equipment and keep it running smoothly? Keep reading to learn how to handle VT1000 pitting like a pro!
Overview of VT1000 Pitting
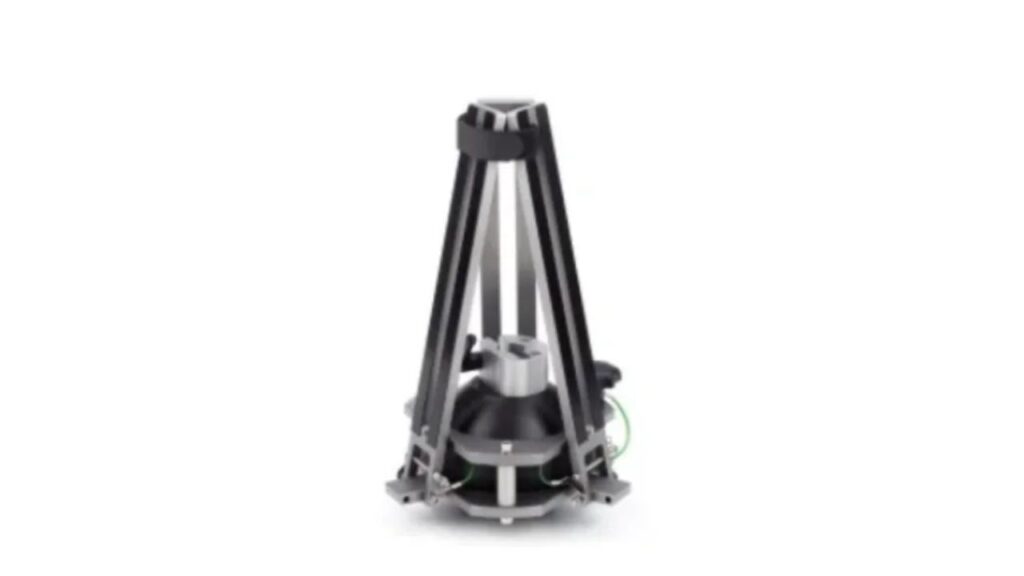
Pitting is a form of corrosion that creates small cavities or holes on the surface of metal parts. This kind of damage is particularly concerning because it can compromise the structural integrity of components, leading to premature failure. VT1000 pitting occurs when the surface of the machine or part corrodes due to chemical reactions, environmental factors, or improper maintenance practices.
Secondary Keywords: corrosion damage, surface wear, mechanical component failure
The VT1000, like many other industrial machines, is susceptible to pitting due to its frequent exposure to harsh environments, chemicals, and moisture. Understanding what leads to pitting can help you maintain your equipment more effectively.
Key Points About VT1000 Pitting
1. Causes of VT1000 Pitting
Several factors contribute to pitting in VT1000 machines:
- Environmental Exposure: Machines that operate in moist or chemically aggressive environments are prone to corrosion. For example, saltwater environments or exposure to industrial chemicals can accelerate pitting on metal surfaces.
- Material Composition: Some materials used in the VT1000 may be more susceptible to pitting. For instance, certain metals that aren’t properly treated or protected are vulnerable to localized corrosion.
- Improper Maintenance: Neglecting regular maintenance and failing to clean and lubricate the machine can lead to increased surface wear and eventual pitting.
Example: If a VT1000 pump is used in a factory setting with high humidity and no proper protective coating, the risk of pitting increases significantly over time.
2. Effects of Pitting on Performance
Pitting may start small, but it can rapidly deteriorate the equipment’s performance:
- Decreased Efficiency: Pitting creates rough surfaces that can lead to drag, friction, and inefficiencies in mechanical operations.
- Increased Wear and Tear: As pitting worsens, it accelerates the wear and tear on components, leading to the need for more frequent repairs or replacements.
- Potential for Component Failure: Deep pitting weakens structural integrity, which can cause parts to fail unexpectedly, leading to costly downtime and repairs.
Statistics: Studies show that pitting corrosion accounts for nearly 40% of failures in industrial equipment due to corrosion, making it one of the most critical issues in mechanical systems.
3. Identifying Early Signs of Pitting
Catching pitting early can save you from costly repairs. Signs to look for include:
- Visible Surface Damage: Look for small pits, holes, or rough patches on metal surfaces during routine inspections.
- Changes in Machine Performance: Unusual noises, increased vibration, or reduced operational efficiency could indicate surface damage.
- Increased Maintenance Needs: If your machine requires more frequent maintenance or lubrication than usual, this could be an early sign of pitting.
Best Practices for Preventing VT1000 Pitting
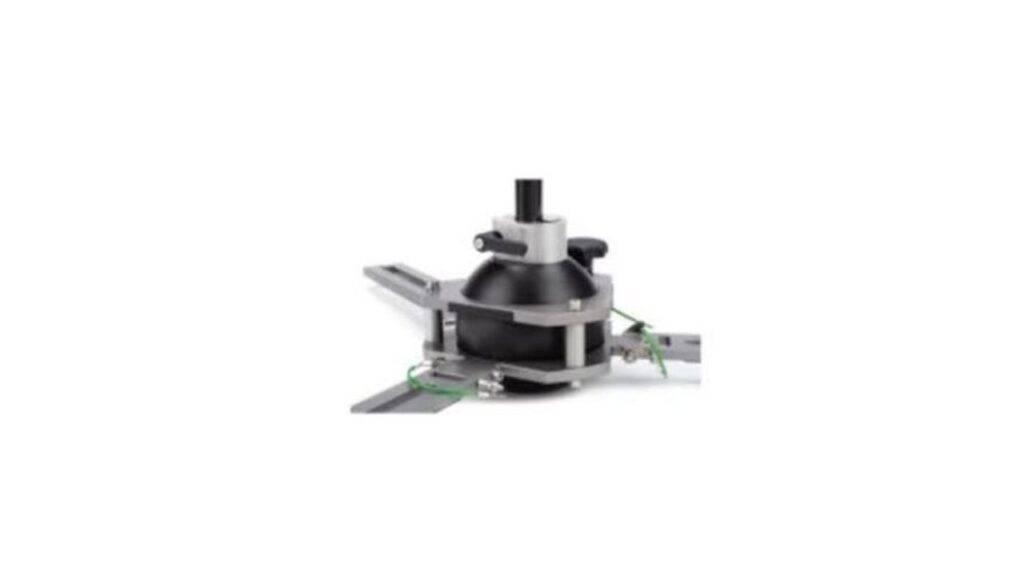
Prevention is the best defense against pitting. Here are actionable steps you can take to protect your VT1000:
1. Regular Maintenance and Inspection
Frequent maintenance is key to preventing pitting. This includes:
- Cleaning: Regularly clean your equipment to remove any dirt, chemicals, or contaminants that could accelerate corrosion.
- Lubrication: Ensure moving parts are properly lubricated to reduce friction and prevent surface wear.
- Surface Inspections: Perform routine inspections to catch early signs of pitting. Use magnification tools or advanced imaging technology to identify small pits before they grow.
2. Protective Coatings
Applying a protective coating can significantly reduce the risk of pitting. Common coatings include:
- Anti-Corrosion Paints: These provide a protective layer against environmental factors like moisture and chemicals.
- Anodizing: This electrochemical process increases the thickness of the oxide layer on metal parts, enhancing resistance to corrosion.
3. Material Selection
Choose materials that are more resistant to corrosion for parts that are at high risk of pitting. Stainless steel or other alloys designed to withstand harsh environments are ideal.
Actionable Tip: Always consult with a material expert before replacing parts to ensure you’re using the most pitting-resistant material for your specific environment.
Common Mistakes to Avoid
Even experienced professionals can make mistakes when trying to prevent or address pitting. Here are some common pitfalls to watch out for:
1. Ignoring Early Warning Signs
Many people ignore the early signs of pitting, thinking the damage is minor. However, pitting can spread rapidly if left untreated, leading to larger problems down the road.
Solution: Take even the smallest signs of corrosion seriously and address them immediately through repair or replacement.
2. Using the Wrong Lubricants
Some lubricants are not suitable for environments prone to moisture or chemical exposure. Using the wrong lubricant can accelerate wear and corrosion, rather than preventing it.
Solution: Use lubricants that are specifically formulated for corrosion-prone environments and adhere to manufacturer recommendations for the VT1000.
Expert Insights and Future Trends
Corrosion-Resistant Technologies: As technology evolves, manufacturers are developing new materials and coatings that offer greater resistance to corrosion. Advanced protective solutions like self-healing coatings and nanotechnology may soon provide even more durable protection against pitting.
Automation in Maintenance: With the rise of the Industrial Internet of Things (IIoT), automated systems can monitor equipment conditions in real-time. These systems will alert operators when early signs of pitting are detected, making maintenance more proactive and less reactive.
Trend Watch: The global cost of corrosion is estimated to exceed $2.5 trillion annually, and industries are increasingly investing in technologies to mitigate these expenses. Expect to see significant innovations in corrosion resistance over the next decade.
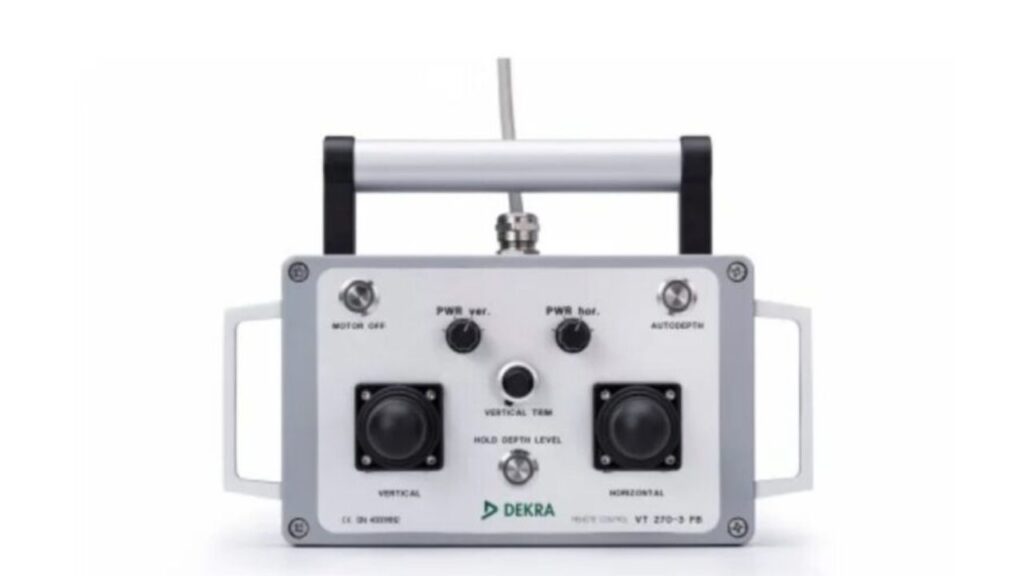
Conclusion: Protect Your VT1000 from Pitting
Pitting may seem like a small issue, but if left unchecked, it can cause significant damage to your VT1000 and other machinery. By understanding the causes, maintaining a regular inspection schedule, and using the proper protective coatings and materials, you can prevent pitting and extend the life of your equipment.
Want to stay ahead of pitting issues? Start implementing these best practices today and ensure your VT1000 runs smoothly for years to come.
FAQs
1. What causes pitting in the VT1000?
Pitting is usually caused by environmental factors like moisture and chemicals, as well as improper maintenance and lack of protective coatings.
2. How do I prevent pitting in my VT1000?
Regular maintenance, cleaning, lubrication, and applying protective coatings are key to preventing pitting.
3. Can pitting be repaired?
Yes, if caught early, pitting can be repaired through surface treatments, but severe pitting may require part replacement.
4. How often should I inspect my VT1000 for pitting?
Routine inspections should be conducted at least quarterly, especially if your equipment operates in harsh environments.
5. What materials are best for preventing pitting?
Stainless steel and other corrosion-resistant alloys are ideal for environments where pitting is a concern.